CNC Precision Parts Factory: Excellence in Metal Fabrication
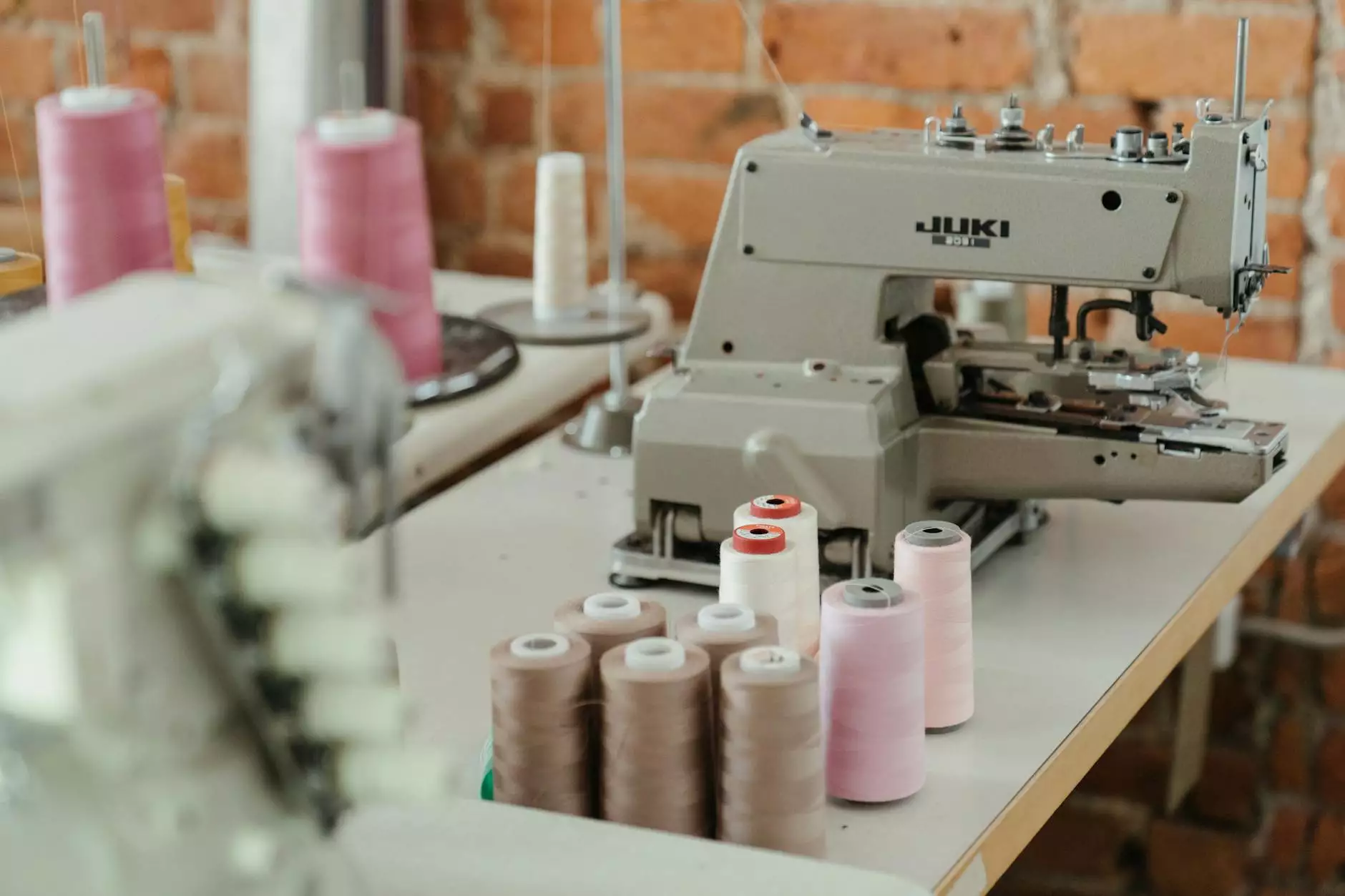
The world of manufacturing is evolving rapidly, driven by the need for precision, efficiency, and quality. In this landscape, a CNC precision parts factory stands at the forefront, providing unparalleled services that cater to a myriad of industrial needs. This article delves into the intricate details of operations within a CNC precision parts factory, showcasing its importance in the broader manufacturing sector.
Understanding CNC Technology
Computer Numerical Control (CNC) technology revolutionized manufacturing by automating machinery and tools through computer programming. This technology allows for the precise machining of parts with minimal human intervention, leading to enhanced accuracy and efficiency. Here’s a breakdown of how CNC technology works:
- Digitization of Designs: Initial designs are created using CAD (Computer-Aided Design) software, allowing for intricate and complex shapes.
- Programming: These designs are then converted into a format that CNC machines can understand, often through CAM (Computer-Aided Manufacturing) software.
- Operation: CNC machines execute the commands through tools that cut, mill, or shape materials according to the programmed specifications.
- Quality Control: Finished components are rigorously inspected to ensure they meet the required specifications and tolerances.
The Role of a CNC Precision Parts Factory
A CNC precision parts factory specializes in producing high-quality components for a diverse range of industries such as aerospace, automotive, medical devices, and electronics. The significant roles played by these factories include:
1. Custom Manufacturing
With the ability to produce tailored parts based on client specifications, CNC precision parts factories provide custom manufacturing solutions that are essential for businesses seeking unique components. This flexibility is vital in accommodating the varied demands of different industries.
2. Mass Production
Beyond customization, these factories also excel in mass production scenarios, ensuring consistent quality across thousands of parts. Using advanced CNC systems, factories can produce large volumes of components with minimal variation, which is crucial for thread count accuracy and assembly line efficiency.
3. Rapid Prototyping
For businesses looking to test new products, the rapid prototyping services offered by CNC precision parts factories enable them to create functional prototypes in a short period. This not only shortens the product development cycle but also reduces costs associated with traditional prototype manufacturing methods.
Benefits of Using a CNC Precision Parts Factory
The benefits of partnering with a CNC precision parts factory extend beyond just production capabilities. Here are a few key advantages:
- Enhanced Precision: CNC machines can achieve tolerances of ±0.001 inches or better, guaranteeing high-quality components that meet stringent industry standards.
- Cost Efficiency: Automation leads to less labor cost and reduced waste, making production not only more efficient but also more affordable.
- Time Management: CNC machines operate faster than manual alternatives, allowing manufacturers to meet tight deadlines without compromising quality.
- Scalability: A CNC precision parts factory can easily scale production volumes based on demand, providing businesses with the agility needed to adapt to market changes.
Key Industries Benefiting from CNC Precision Parts
Numerous industries rely heavily on the services of a CNC precision parts factory. The key sectors include:
Aerospace
Aerospace components must adhere to stringent weight and durability requirements. CNC precision parts factories produce complex aerospace parts such as brackets, fittings, and actuators, ensuring that they can withstand the rigors of flight.
Automotive
In automotive manufacturing, numerous components require precision-engineered parts for optimal performance. CNC factories manufacture everything from engine components to interior fittings, contributing to the overall safety and efficacy of vehicles.
Healthcare
In the medical device industry, precision is paramount. CNC precision parts factories produce surgical instruments and implants that require exact dimensions to ensure patient safety and product reliability.
Process of CNC Machining in a Factory
The CNC machining process in a precision parts factory can be broken down into several stages:
1. Design Consultation
Initial discussions with clients help define requirements and specifications. Engineers assess the design feasibility, material selection, and potential manufacturing challenges.
2. CAD Modeling
Once the specifications are defined, a CAD model is created. This digital representation includes precise dimensions and geometries required for the final product.
3. CAM Programming
CAM software translates the CAD model into machine-readable instructions that control the CNC machinery.
4. Machining
The CNC machine fabricates the part using various techniques such as milling, turning, or laser cutting, depending on the complexity and material.
5. Post-Processing
After machining, parts often require finishing techniques like plating, painting, or etching to enhance their functionality and aesthetics.
6. Quality Assurance
Final products undergo rigorous quality assurance processes, including the use of precision measuring tools to ensure that they meet all specified tolerances.
Challenges Faced by CNC Precision Parts Factories
While CNC precision parts factories offer numerous benefits, they also face various challenges that must be managed effectively:
1. Technological Advancements
Keeping up with rapid technological advancements requires ongoing investment in new equipment and training to ensure the workforce is skilled in the latest CNC technologies.
2. Material Selection
Choosing the appropriate materials for each job can be complex, as it can significantly affect the performance and cost of the final product. Factories must stay informed about new materials and their properties.
3. Maintaining Accuracy
Ensuring consistent accuracy and quality across all parts is a challenge, particularly when scaling production. Implementing thorough quality control processes is essential.
4. Supply Chain Management
Managing a reliable supply chain for materials and components is crucial. Disruptions in the supply chain can lead to delays in production schedules and increased costs.
Future Trends in CNC Precision Parts Manufacturing
The landscape of CNC precision parts factories is continuously evolving. Here are some emerging trends shaping the future:
1. Automation and Robotics
Increasing automation through robotics enhances production efficiency and safety, reducing labor costs while maintaining quality. Factories are likely to integrate more robotic solutions to streamline operations.
2. Advanced Materials
The development of advanced materials, such as composites and lightweight alloys, will enable CNC factories to produce even more specialized parts that meet modern applications' demands.
3. Sustainable Manufacturing Practices
Environmental concerns are driving the need for sustainable practices in manufacturing. CNC precision parts factories are exploring waste reduction, energy efficiency, and recycling of materials.
4. Smart Manufacturing
The integration of the Internet of Things (IoT) in manufacturing processes allows for better monitoring, predictive maintenance, and greater operational efficiency through data analysis.
Conclusion
A CNC precision parts factory is a vital component of modern manufacturing, delivering high-quality and highly precise components tailored to the needs of diverse industries. By harnessing the power of CNC technology, these factories not only ensure precision and efficiency but also play a critical role in innovation and growth across various sectors. As technology continues to evolve, embracing these advancements will undoubtedly set the path for the future of manufacturing.